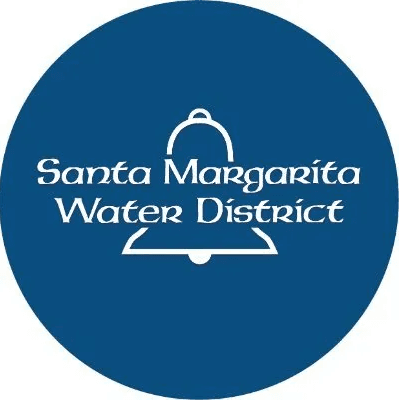
Santa Margarita Water District
Utility Technician (Mechanical Maintenance)
Meet Santa Margarita Water District
Santa Margarita Water District is a dynamic, forward-thinking agency dedicated to delivering high-quality potable water, recycled water, and wastewater services to its 200,000 customers across Southern Orange County. As one of the region’s largest and most impactful utilities, we are committed to the highest standards of transparency, innovation, and environmental stewardship.
Our people drive our progress, innovation, and results. Our collaborative, human-first culture fosters the sense of fun, comradery, and a rewarding sense of purpose as we do work that matters.
Dynamic teams of intelligent individuals work collaboratively to achieve SMWD’s goals and solve challenges with a common aim that fosters a unique bond that is not often found in governmental agencies.
Santa Margarita Water District’s values include:
- Exemplary service excellence
- Intelligent innovation that is forward-thinking and adaptive
- Ethical fiscal responsibility and transparency
- Environmental and resource stewardship
- Employee development and leadership training
- Building relationships that strengthen communities
The Santa Margarita Water District has an opening in its Operations Department on the Mechanical Maintenance Crew. The ideal candidate will have experience working in and around Recycle and Wastewater systems. Primary functions include:
- Operating, repairing, and maintaining District facilities; pumps and motors; various types of valves, and chemical feed equipment.
- Function testing of alarms; troubleshooting operational issues and responding to alarms.
- Experience working with a SCADA system to monitor, gather information and make operational decisions regarding the information available.
- Ability to plan work from blueprints, drawings, sketches, or instructions; maintain records, databases, spreadsheets, and other reports.
- Ability to actively participate in Confined Space Entry.
- Familiarity with mechanical seals and installation on different pump configurations.
- Prioritizing safety.
- Ability to diagnose mechanical failures and rebuild as necessary.
- Experience with Microsoft applications, MMS systems, and ability to communicate effectively.
- Knowledge of fabrication/welding is a plus.
- Wastewater treatment plant experience is a plus.
Class specifications are intended to present a descriptive list of the range of duties performed by employees in the class. Specifications are not intended to reflect all duties performed by individual positions
JOB SUMMARY
Under direct supervision, learns to perform both routine and semi-skilled heavy, physical work in the construction, maintenance, mechanical repair and operation the District infrastructure and related structures and appurtenances; operates a variety of hand and power tools; performs related work as assigned.
DISTINGUISHING CHARACTERISTICS
A Utility Technician is the working level position in the Systems/Utility Operator/Mechanic class series and is characterized by the performance of tasks of limited scope, involving practical application of established procedures and policies. Utility Technicians are normally trainee positions with the incumbents advancing to Systems/Utility Operator/Mechanic as the difficulty and complexity of their duties increase and when they have received cross training in a variety of mechanical repair and operation of the District’s systems. The progression of a Utility Technician to a Systems/Utility Operator/Mechanic includes a combination of obtaining the required certification and/or license and an evaluation of employee skill and performance levels by management.
Essential Functions:
ESSENTIAL FUNCTION STATEMENTS
The duties listed below are intended only as illustrations of the various types of work that may be performed. The omission of specific statements of duties does not exclude them from the position if the work is similar, related or a logical assignment to the class.
- Learns and assist in installing, maintaining and repairing District infrastructure, including, but not limited to, pipelines, taps, laterals, valves, meter services, fire hydrants and related appurtenances and treatment plant equipment.
- Performs construction and maintenance work on District buildings and facilities as assigned including, but not limited to, concrete work, plumbing, roofing, framing and drywall.
- Learns and assists in repairing, rebuilding and installing sewage pumps, natural gas engines, a variety of electric and gas driven air compressors, handling units and associated equipment; performs routine preventative maintenance.
- Excavates and shores trenches; backfills cuts, patches, repairs and resurfaces streets; cleans up work sites; installs, raises, lowers and grades valve cans.
- Learns and assists in servicing and maintaining pump stations, valves, chemical feed equipment, telemetry systems, cathodic protection systems and related equipment; performs routine repair work as assigned.
- Paints and applies protective coatings to District infrastructure including pumps, pipings, valves, fire hydrants, and walls.
- Learns and assists in operating and maintaining valves, regulators chemical feed and pumping stations, reservoirs and related equipment and facilities; monitors gauges and telemetry, and records readings.
- Learns and assists in repairing and maintaining District infrastructure, such as, mains, laterals, catch basins, manholes, lift stations, pressure lines and related structures; loads and unloads trucks, cleans up work sites upon completion of job; operates and performs routine preventive maintenance on pumps, valves and related lift station and plan equipment; reads and interprets plan, maps and prints.
- Learns and assists in flushing and cleaning collection systems; applies herbicides, foams and other chemicals to deroot, degrease and unstop lines; installs and removes flow meters.
- Observes safe work methods and safety practices related to work; cones and flags work sites to secure from traffic; shores trenches; uses appropriate safety equipment; operates and maintains a wide variety of hand tools related to the work, including spaders, tampers, breaking guns, jackhammers, concrete saws, etc.; learns to operate a variety of trucks and equipment; inspects vehicles and performs minor maintenance, reports needed repairs.
- Fuels and lubricates vehicles and related equipment such as gas powered and electric carts; operates assigned vehicles on various assignments skillfully and safely; observes safe driving practices; operates and maintains a wide variety of hand and power tools and equipment related to work assignments.
- Learns and assists in repairing, rebuilding and/or installing equipment in treatment plants and field facilities; works in confined spaces using proper safety equipment, performs routine preventative mechanical and electrical maintenance as assigned.
- Maintains fire protection equipment including sprinkler systems, fire alarms and fire extinguisher inspections.
- Performs ground-keeping functions requiring the use of gas powered equipment such as leaf blowers, mowers, string trimmer and tractors.
- Reads and interprets maps schematics, plans, blueprints and specifications.
- Completes basic records related to work performed; may collect and enter data into computer system.
- Responds to emergency situations during off-hours as required; participates in standby duties at the sole discretion of the District.
- Performs related duties and responsibilities as required.
Requisite Abilities/Qualifications & Guidelines:
Ability to:
- Perform a variety of routine construction, repair, and maintenance tasks.
- Work under routine and emergency conditions, sometimes in severe weather.
- Work efficiently and safely with others.
- Understand and follow instructions and directions.
- Perform a wide variety of physically strenuous tasks.
- Enter data in computer system.
- Safely operate heavy construction and repair equipment.
- Learn to operate and properly repair valves, fittings and hydrants.
- Read, interpret and understand blueprints and construction drawings.
- Learn to perform a variety of mechanical repairs.
- Maintain records.
- Maintain and repair equipment and tools.
- Operate and maintain a variety of hand and power tools and equipment.
- Properly place cones, barricades and warning devices and direct traffic flow at job sites.
- Exercise sound judgment and initiative in the performance of assigned tasks.
- Meet the physical requirements established by the District.
- Knowledge of proper painting and coating techniques including the preparation of metals, woods, concrete and stucco.
- Safely operate a forklift.
- Operate and maintain tools and equipment used in painting such a needle scaler, sand blaster and paint spray equipment.
Knowledge of:
- Methods, techniques, tools and equipment used in the installation, maintenance and repair of mechanical equipment and machinery common to a large water works system.
- Machine shop procedures and practices.
- Pipe materials, pipe fittings and pipefitting tools and methods.
- Safe Drinking Water Act, AWWA, Title 22 of California’s Water Recycling Criteria and relevant state and federal regulations.
- Water mathematics.
- Methods for the safe operation of light, medium and heavy duty motorized power equipment, as certified.
- Knowledge of traffic control practices and requirements.
- Principles and practices of sound business communication; correct English usage, including spelling, grammar and punctuation.
- Safety Policies and safe work practices applicable to work.
- Records management, recordkeeping, filing and basic purchasing practices and procedures.
- Uses and operations of computers, standard business software and specialized database and spreadsheet applications.
Additional Information:
QUALIFICATIONS
Any combination of experience and training that would likely provide the required knowledge and abilities is qualifying. A typical way to obtain the knowledge and abilities would be:
Education, Training and Experience:
Equivalent to graduation from high school and some experience as a laborer in construction, mechanical or maintenance work.
Licenses; Certificates; Special Requirements:
- Annual certification for CPR, First Aid, Confined-Space Entry and use of Self-Contained Breathing Apparatus (SCBA) per OSHA requirements are required.
- Possession of a Class C California driver’s license (unless a Class A or B is specified below), a satisfactory driving record and the ability to maintain insurability under the District’s vehicle insurance program.
- D1 Certificate from SWRCB (within 12 months of hire/promotion)
PHYSICAL AND MENTAL DEMANDS
The physical and mental demands described here are representative of those that must be met by employees to successfully perform the essential functions of this class. Reasonable accommodations may be made to enable individuals with disabilities to perform the essential functions.
Physical Demands
While performing the duties of this job, the employee is regularly required to sit, walk and stand; talk and hear; use hands to finger, handle, feel or operate objects, tools or controls; reach with hands and arms; perform repetitive movements of hands or wrists; climb or balance on ladders or stairs; stoop, kneel, bend at the waist, crouch or crawl; and have the ability to detect odors. The employee is frequently required to lift up to 50 pounds and frequently up to 100 pounds with assistance.
Specific vision abilities required for this job include close vision, distance vision, use of both eyes, depth perception, color vision and the ability to adjust focus.
Employees in this class may be periodically required to wear Self-Contained Breathing Apparatus (SCBA). In accordance with OSHA regulations, employees are prohibited from having facial or head hair that impairs the effectiveness of respirator equipment. Reasonable accommodations may be made to enable individuals with disabilities to perform essential duties of the class as they relate to this requirement.
Mental Demands
While performing the duties of this class, an employee uses written and oral communication skills; reads and interprets data, information and documents; analyzes and solves problems; uses water math; learns and applies new information and skills; responds to emergency situations; and interacts with others encountered in the course of work.
WORK ENVIRONMENT
The employee works in a shop and field environment where the noise level is usually moderate. The employee works in outdoor weather conditions; extreme heat or cold; wet, humid conditions; in confined spaces; on ladders/scaffolding or in high, precarious places; on uneven or slippery surfaces; near moving mechanical parts; near moving equipment; and near heavy traffic. The employee is exposed to fumes or airborne particles, toxic or caustic chemicals, and biological hazards. The employee is occasionally exposed to loud or prolonged noise and equipment with heavy vibrations. The employee may be at risk of electrical shock.
The employee may be required to work various shifts and standby at night, on weekends and holidays as needed.
Visit our career page here to apply!